
Thermal spraying
KVT coating methods
The right approach to every application
Thermal spraying is a proven and successful technology that has been used in virtually all branches of industry for over a century.
Thermal spraying is used to guard components and assemblies against wear, corrosion, heat or combinations of these influences. In all thermal spraying processes, tiny particles of the coating material are first heated and accelerated in a spray gun and then sprayed onto the substrate surface that is to be coated. When the particles have reached a sufficiently high temperature and speed, they form a coating that exhibits the required properties and adhesive strength.
By combining base materials with a large number of spray additives, it is almost always possible to find the ideal solution to prevent wear. The coating method used also affects the choice of the coating system.
Using expanding combustible gases, an oxy-acetylene flame is used to fuse an additive powder onto the prepared surface of the workpiece. If necessary, an additional gas (such as argon or nitrogen) can be used to accelerate the powder particles.
A distinction is drawn between self-fluxing and self-adhesive powders. Self-fluxing powders always require additional thermal treatment. This fusion method primarily uses oxy-acetylene torches.
Benefits:
- A wide variety of spraying materials
- The coating system is impervious to gases and liquids
- Non-porous coating layers
- Strong wear-resistance when subject to linear, concentrated and distributed stresses
- Powerful adhesive strength
- Metallurgical bond to the base material
- Coating lends itself to subsequent treatment (turning, milling, grinding and lapping)
- Strong resistance to corrosion by caustic solutions, weak acids and aqueous solutions
Drawbacks:
- Partial coatings are not possible
- Chrome steel is not suitable for metallurgical bonding
- The base material is subject to significant temperature stresses
- The component geometry is subject to restrictions
Coating thickness: 0.3–0.8 mm
Coating adhesion: Very good diffusion
Temperature stress: Very high (up to 1,050 °C)
Base materials: Stainless steel/duplex stainless steel, nickel-based alloys
Treatment: Coatings can be turned, ground and lapped
Compared to flame spraying, the HVOF method accelerates the process gas to almost supersonic speeds. An additive powder is fed into the center of the combustion chamber. Continuous burning of the oxyfuel mixture creates high pressure within the chamber and combines with a downstream expansion nozzle to generate a high-velocity gas beam that also accelerates the sprayed droplets to a high speed of up to 800 m/s.
Benefits:
- Low thermal stress for the base material
- Very hard coatings can be achieved
- Strong wear-resistance when subject to linear stresses
- Tensile strength in conjunction with tungsten carbide and chromium carbide
- > 70 MPa
- Material-independent coatings
- Partial coatings are possible
- Coatings can be ground and polished
- Sprayed coatings are highly impermeable
- Very low porosity (< 2%)
- Minimal metallurgical changes
- Thin and very accurately dimensioned coatings
Drawbacks:
- Microporous coatings of 1–5%
- Low concentrated stress tolerance
- Poor shock-resistance at edges, poor notched impact strength
- Diminished corrosion-resistance
Coating thickness: 0.1–0.3 mm
Coating adhesion: Good adhesive properties (>70 MPa)
Temperature stress: Low (100–300 °C)
Base materials: All metals
Treatment: Coatings can be ground and lapped
Laser deposition welding uses optical components to guide the laser beam onto the component surface. A focus lens concentrates the beam into a focal point to heat the base material. At the same time, a coaxial inert gas powder nozzle is used to feed the powder material into the process with an inert carrier gas and melt it onto the surface. Metallurgical bonding with the substrate creates a very powerfully adhesive coating.
Benefits:
- Low heat input into the component, resulting in minimal warpage and a small heat-affected zone
- No need for elaborate subsequent treatment of the component
- Very good coating adhesion due to metallurgical bonding (i.e. focused bonding with the substrate surface thanks to a precisely controlled process)
- Very precise coating contours even for complicated workpiece shapes
- High powder efficiency in excess of 70%, making this an ecofriendly technology
- Partial coatings are possible
- Complex geometric structures are possible
- Good shock-resistance at edges, good notched impact strength
- Good options for subsequent treatment (turning, milling and grinding)
Drawback:
- Can be used only for weldable materials
Coating thickness: Individual coatings up to 2 mm thick; multiple layers possible
Coating adhesion: Very good adhesion due to metallurgical bonding
Temperature stress: Low (100–300 °C)
Base materials: Weldable steels and alloys
Treatment: Coatings can be turned, ground and lapped
Applications: Coatings to improve wear-, corrosion- and heat-resistance under extreme conditions (high pressure, long service lives and extreme wear) in areas such as valve engineering, the drilling industry, mechanical engineering, engine construction etc.
Why KVT?
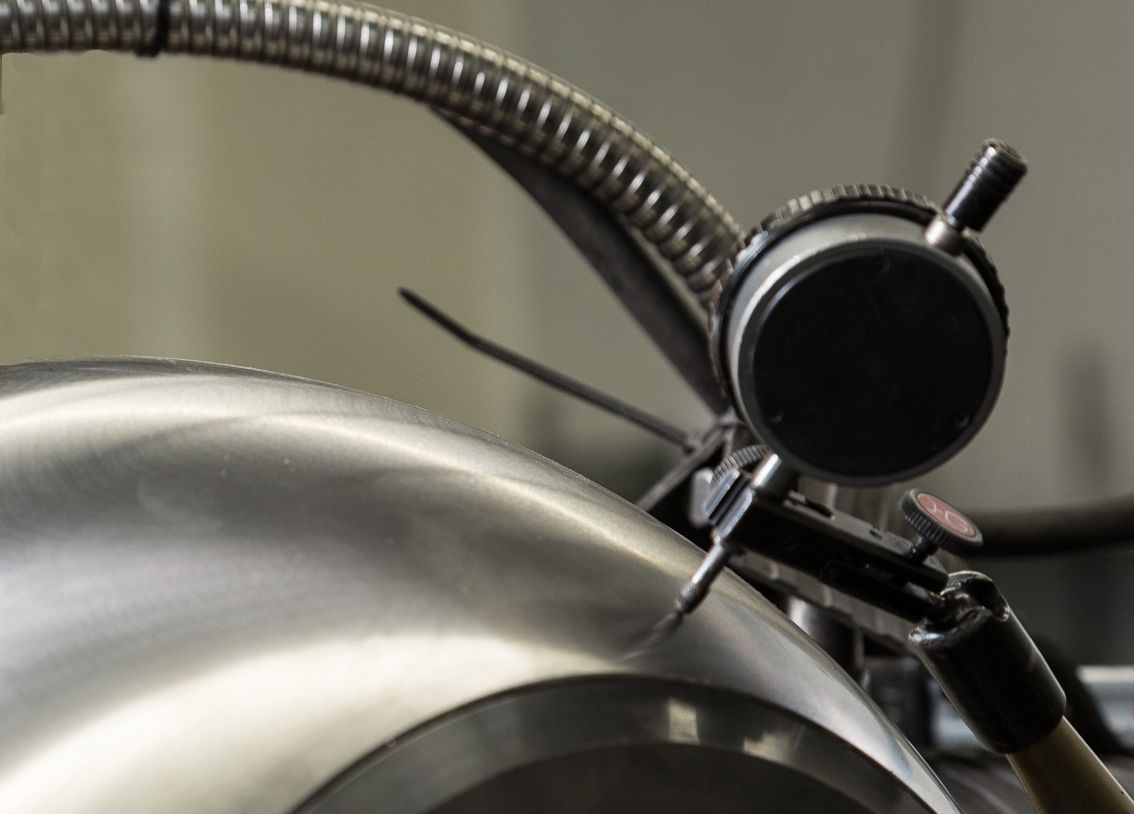
What sets us apart
Whenever abrasion, high temperatures, high pressure levels, large numbers of cycles and high flow velocities are critical factors, we are the people to talk to.
More detailsDownloads
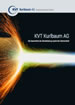
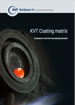