
Sample applications
Drilling industry
The drilling industry demands extremely high standards of quality and process stability, especially to protect the environment as gas and oil are extracted.
KVT Kurlbaum AG plays an important part in ensuring compliance with these standards and keeping drilling both efficient and cost-effective.
Why KVT?
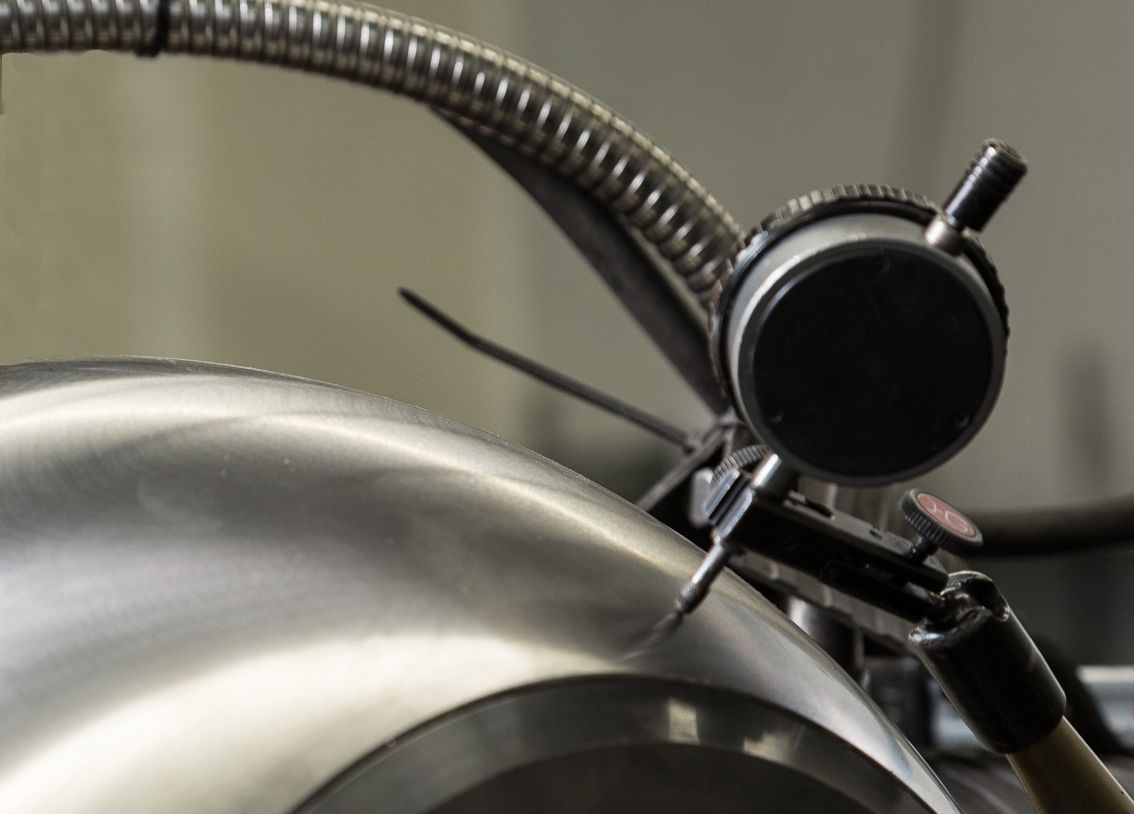
What sets us apart
Whenever abrasion, high temperatures, high pressure levels, large numbers of cycles and high flow velocities are critical factors, we are the people to talk to.
More detailsDownloads
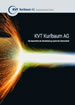
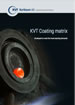